By Joe Bailey, Food and Beverage Product Lifecycle Management Subject Matter Expert.
I hear it frequently with food and beverage companies, that they find themselves often reacting to product issues, acting as a firefighter, as they struggle to proactively see and remove obstacles before they occur. They focus on the issue that is currently screaming the loudest. For many reasons companies find themselves in this situation instead of being able to proactively prevent issues and seize on strategic opportunities. Three common reasons include:
1. Lack of accessible and detailed product data visibility
Companies often find product information all over in disconnected locations like spreadsheets and email not easily accessible and visible. Even companies using multiple product data software applications find these systems act as satellite systems communicating minimal to no information with each other. This presents major challenges to see a full picture of what is going on and what is on the horizon.
2. Lack of centralized collaboration and communication both in and outside of product systems
With product lifecycle management, users in different departments can struggle working together and sharing information especially if they don’t find value in it for themselves and work in different systems. Standardized system and business processes can help facilitate collaboration, especially if leaders see and facilitate the vision. However, when systems don’t share information and standardized business processes don’t ensure active collaboration, duplication of effort and gaps and missed opportunities surface.
3. Gaps communicating and sharing information with business partners
Product specifications in many companies are shared via email for co-manufacturers and customers and can be difficult to track what has been sent and to who. Those on the receiving end can also find it challenging to know what the latest version is, how many documents they received and to organize everything being sent to them. Similarly, suppliers share documents and information for food and beverage manufacturer products, and it can be challenging to ensure that your organization is aware of that information and that it gets updated and transferred effectively to your PLM, ERP and other application(s).
Dynamic FRM™ facilitates collaboration and effective management of product data throughout the product lifecycle. Users work together on product ideas, consistent processes can be followed, tasks are recorded and completed, and relevant product information is captured in a centralized platform that communicates to other applications such as ERP and LIMs systems.
Multiple dashboards can be created in various formats covering key performance indicators:
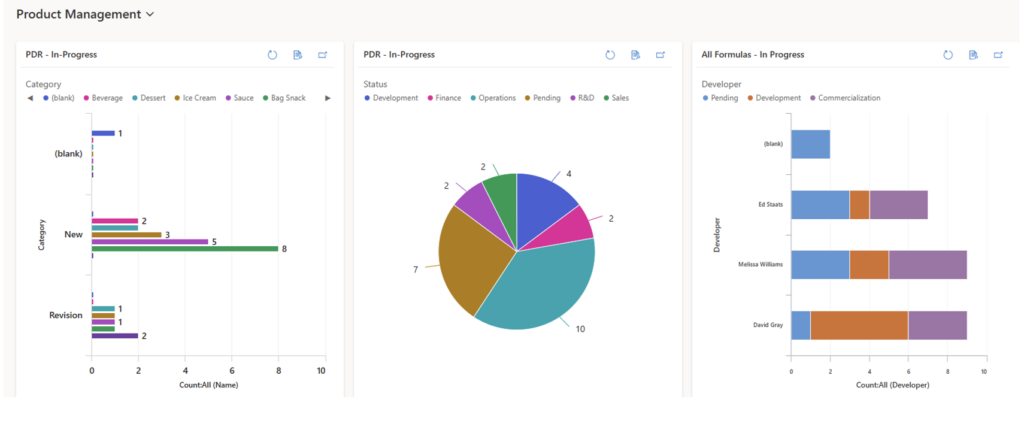
Group or individual views and charts can be created and shared. The interactive views and charts allow users to drill down into product details in real-time, helping uncover root cause. Users can also collaborate via Teams within the application if desired.
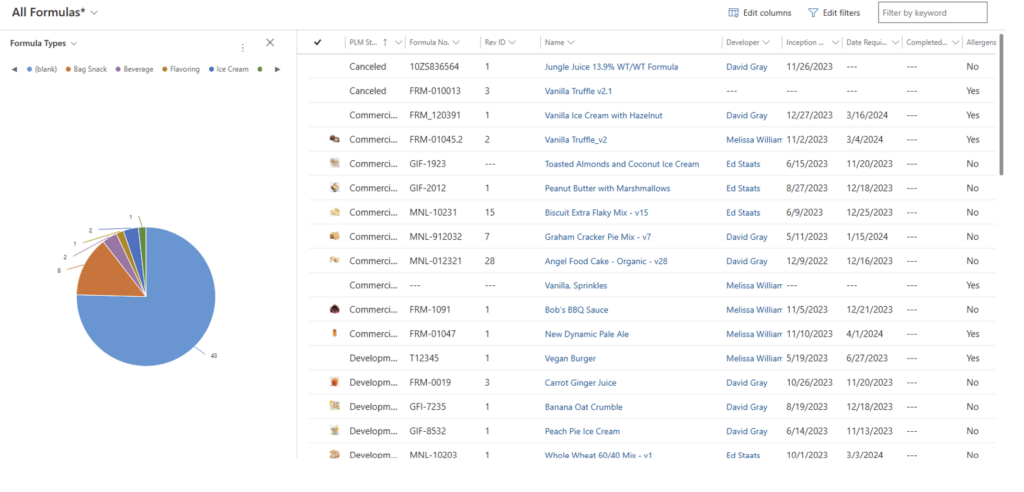
Dynamic FRM™, built on the Microsoft platform, uses Power BI to unlock detailed product insights, both within Dynamic FRM and if desired, other related systems as well (i.e. ERP, LIMS, etc.). Users can compare product attributes such as ingredient statements and identity preserved characteristics on as many or as little items, formulas and versions desired. This helps in finding potential production efficiencies such as introducing a new allergen or adding an abnormal testing frequency to a production line.
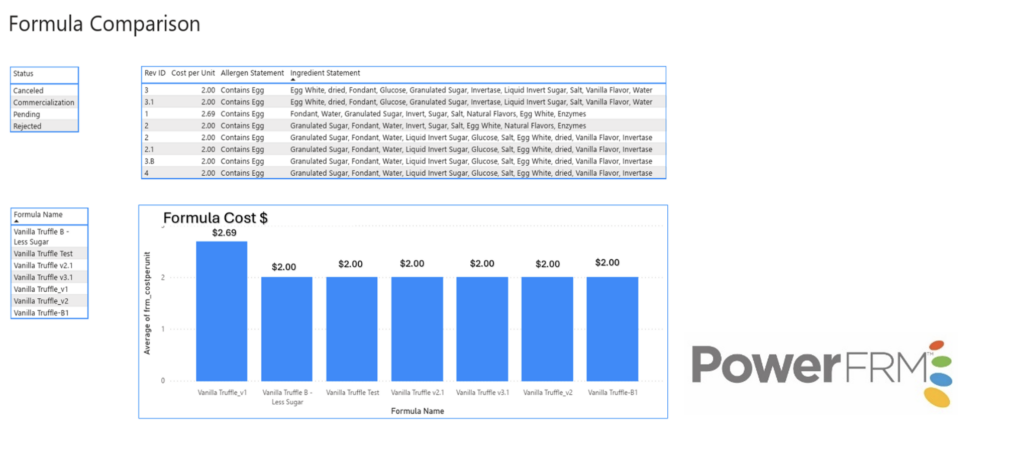
Dynamic FRM™ can also automatically provide specifications and other product data to co-manufacturers and/or customers through a secure portal. This eliminates the need for email and streamlines the process. Supplier documentation and communication can also be managed through a secure portal.
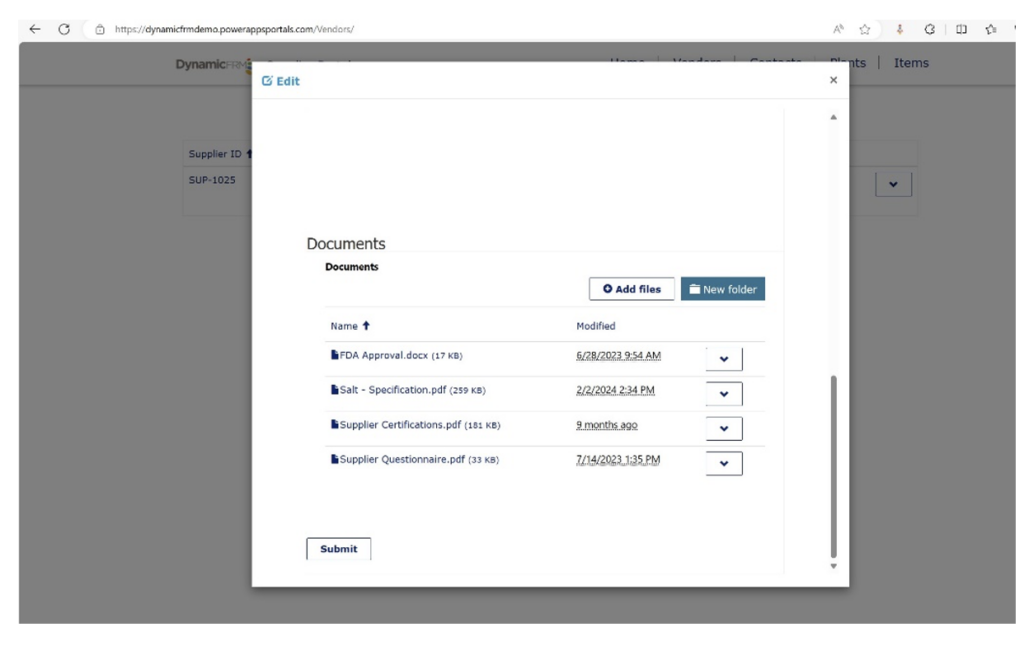
Join the Dynamics FRM™ Community
If you found this blog helpful, subscribe below to receive our monthly updates.